FAQ's
General questions
I cannot achieve the airflow from my ducted fan coil
A shortage of airflow is more often than not caused by excessive external resistance. The following should be checked
1. Is the filter dirty? Routine maintenance procedures should be carried out regularly and in line with installation manual
2. Dampers have been improperly balanced creating unwarranted excessive resistance
3. One or more of the fans are not running.
3. There are not enough return air grilles which can especially be an issue in crowded open plan spaces
4. Check pitot traverse results and Hood k factor to ensure it is correct
To check the external resistance an average static pressure should be measured across all outlet ducts (+be), close to the unit and prior to the dampers against the static pressure on the inlet to the unit (-ve)
My ducted unit seems to be excessively noisy
Check the external static pressure as described below
To check the external resistance an average static pressure should be measured across all outlet ducts (+be), close to the unit and prior to the dampers against the static pressure on the inlet to the unit (-ve)
Ensure no foreign object are caught in the fans
Excessive noise will be created if units are installed too close together. If 2 similar noise sources are in close proximity this could as much as 3db, 4 sources, 6db.
The installation environment is not a ‘typical installation’ which would have been allowed for in NR selections. Increased reflective surfaces, a reverberation time that isn’t suitable for application, amount of glazing all have an effect on the sound pressure levels and resultant NR readings.
My cassette unit seems to be excessively noisy
Check filter is not clogged and replace if necessary
Ensure outlet vanes are not closed or have vastly reduced openings as this will restrict airflow and cause excessive noise
Ensure fan is not catching on the cowl. This can be caused during installation and should be check prior to applying power.
My wall mounted unit seems to be excessively noisy
The most common cause on these units is foreign bodies trapped in the fan. The top of the unit creates a convenient shelf for tools and odd bits which if dislodged will fall into the fan area. Please ensure this is fully clear. Damage to impeller or motor will not be covered by warranty.
Water is dripping from my ducted unit chassis
Ensure the unit is installed level
Check to ensure water is draining away from the drain tray,
1. If a gravity drain is been operated is there enough fall over distance to achieve adequate drainage
2. Is there a blockage in the drain path that could be causing condensate to back up into the fan coil
3. Is there an overproduction of condensate in the drain tray? Check there is no leak on the unit leading to an excessive amount of water to gather within the tray.
The fans in a ducted fan coil create a negative pressure. On condensate pipework, especially gravity systems a suitable air break and p trap should be used to allow the flow of water from the unit. Failure to do so can cause excessive back up of water in the tray. This can especially happen when high inlet static pressures are present.
There are a number of ways to resolves this.
1. A suitable P trap should be used. This is the correct solution but if this isn’t possible steps 2 and 3 can help
2. A condensate pump can help to overcome the pressure
3. Reduce airflow to 25% every 30mins for a short period of time, if possible on BMS (if applicable) which will reduce negative static pressure and allow full drainage
Water is discharging from vanes on a cassette unit
This is more often than not when units are installed in high humidity areas which they were specified for and high latent (production of condensate) duty occurs. This allows water carry over from the internal condensate reservoir at higher fan speeds.
Lower fan speed and see if it eliminates the problem
Check unit is installed level
Check to ensure water is draining away from the drain tray,
1. If a gravity drain is been operated is there enough fall over distance to achieve adequate drainage
2. Is there a blockage in the drain path that could be causing condensate to back up into the fan coil
3. Is there an overproduction of condensate in the drain tray? Check there is no leak on the unit leading to an excessive amount of water to gather within the tray.
If it continues, help should be sought from Quartz technical please call 01484 405630
Fan motor within fan coil unit is not running
All of our DC motors within our fan coil units require a 230VAC supply along with a 0-10VDC fan speed signal, each unit is supplied with a project specific wiring diagram which shows the connection details for these supplies. Any electrical checks done by referencing this wiring diagram should be undertaken by a competent person only.
Electrical characteristics for fan coil supply
Each model of any fan coil has its individual load characteristics available in our technical manuals available in the download section of our website. All Quartz fan coils require a 230VAC 50Hz single phase supply, please note in cases where fan coils are designated to be set up in a master/slave configuration all efforts should be taken to ensure master unit and subsequent slaves are supplied on the same electrical phase to reduce any chance of potential difference between units.
Coil connection details for incoming pipework
All connection sizes and incoming pipework centres are detailed in our technical manuals available in the download section of our website.
Is it possible to fit condensate pumps once the units have been installed
All of our provided units allow for optional retro fitment of condensate pumps if required. Pump kits can be ordered from Quartz and provided with installation instructions. Please see spares catalogues for available options and part numbers
Where is my wiring diagram for my unit
All Quartz fan coils will be provided with a project specific wiring diagram, this is located on the unit either on the underside of the lid from the electrical enclosure or on the unit itself dependant on model of fan coil.
Where is the serial number of my unit
The unit serial number is located on the silver data sticker located on the unit chassis
Where can spares information be found
All spares catalogues for each fan coil model can be found under the downloads section of our website. If for any reason you cannot locate the spare you require from these lists contact us on 01484 405630 or at sales@quartz.co.uk
RDG controllers
What cable type should be used to wire from the controller to FCU
The RDG controller can accommodate a control cable of up to 1.5mm (note this does not need to be screened) up to a maximum distance of 60 metres. All wiring undertaken should comply with local regulations and standards.
How can these controllers be wired in a master/slave configuration?
One RDG controller can be used to control multiple units (up to a maximum of 5) by wiring from the wall mounted RDG into the first required controls enclosure of the unit and then using a “daisy chain” or in series method, wiring into subsequent fan coils one after another. This method will cause all units wired in this design to react the same with regards to fan speed and heating/cooling outputs as demanded by the RDG controller.
Is it possible to wire a fire alarm/timer circuit into the system to cut the FCU outputs on demand?
Terminals D1 & GND on the mounting plate of the controller are a set of dry contacts that can incorporate external timers or alarm activations to inhibit all outputs from the wall controller. By default, this is a Normally Open contact but can be changed to Normally Closed by accessing P42 within the parameter control menu.
What should the DIP switches be set to on the rear of the controller?
1. 2 Pipe system (cooling only by default)
DIP switch 1 – ON DIP switch 2 – OFF DIP switch 3 – OFF
2. 2 Pipe system with additional electric heat
DIP switch 1 – OFF DIP switch 2 – ON DIP switch 3 – ON
3. 4 Pipe system (heating and cooling)
DIP switch 1 – OFF DIP switch 2 – OFF DIP switch 3 – ON
4. 4 Pipe system with additional electric heat (RDG100 only)
DIP switch 1 – OFF DIP switch 2 – ON DIP switch 3 – ON
What extras are available with the RDG Range?
Infra-red remote – IRA211 Quartz P.N 485236
Wall sensor – QAA32 Quartz P.N 48030477
Return air sensor – QAH11.1 Quartz P.N 48002250
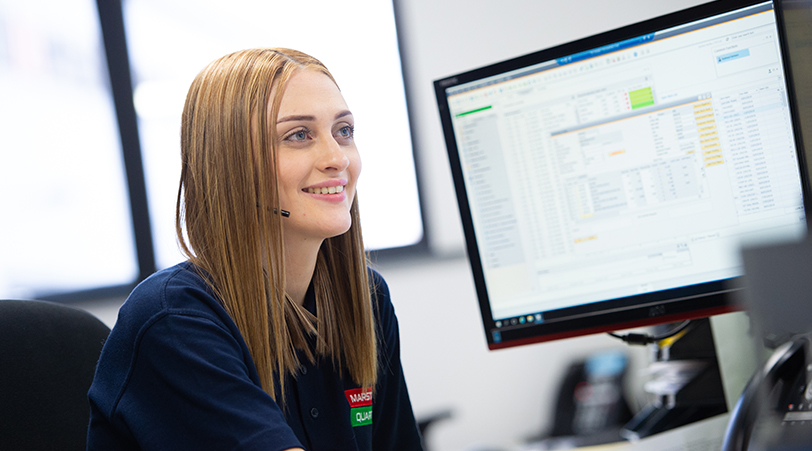